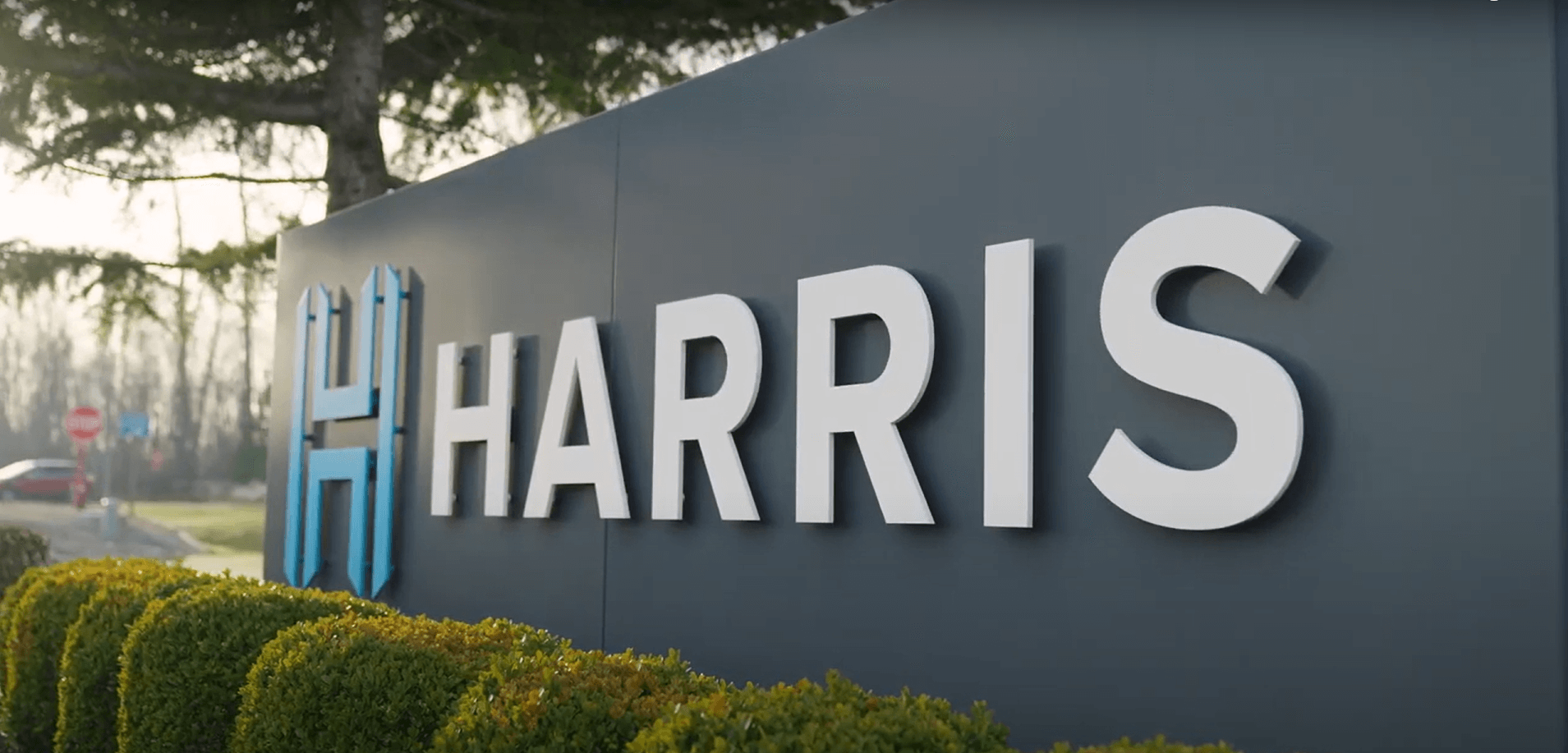
State-of-the-Art Prefabrication Shop in Bellingham, WA Video
(ST. PAUL, Minn.) – Leading national mechanical contractor Harris is highlighting its state-of-the-art prefabrication shop in Bellingham, Washington in a new video. The piece shows how Harris is answering critical trends in the construction industry to deliver shorter project schedules and answer workforce shortages.
Harris’ Pacific Northwest shop supports projects by crafting HVAC ducts, HVAC piping, plumbing piping and purity gas piping. The video details how the 41,000-square-foot facility, which houses its sheet metal, plumbing and pipe fabrication shops, helps Harris deliver unmatched value to customers. This behind-the-scenes look demonstrates how Harris’ certified experts manufacture every component to exact specifications using industry-leading equipment. Advanced technology like building information modeling (BIM) is enabling increased use.
Harris’ prefabrication approach focuses on innovation, efficiency and safety. By manufacturing components and assemblies in an environmentally controlled shop, Harris can maintain safer, more efficient job sites. Shifting work from the field to an offsite location and utilizing BIM allows Harris to reduce safety risks in the field, minimize material waste, keep job sites clean, decrease install time, save labor costs and ensure projects and budgets stay on track.
The video also demonstrates how Harris’ Bellingham shop can adapt to challenges and handle unexpected items on a quick turnaround, often in less than 24 hours. This local facility’s average fabrication is 64 pounds per hour. With this premier fabrication shop, Harris has the expertise and resources to develop advanced solutions and deliver results.
The Bellingham prefabrication shop is one of the nine Harris manufacturing facilities across the United States which allows the industry leader to meet and exceed customer expectations on local and national projects. Harris uses a hub-and-spoke prefabrication strategy with the hub being the project site and the spokes branching out to its designated prefabrication shops, as well as to co-fabrication sites on-or-near the project. In this process, bulk materials are fabricated in a main facility and then flat-packed and shipped to a co-fabrication site. Final assembly is completed and the prefabricated components and modules are delivered to the building or facility, often being lifted into the air and immediately installed.
Harris works on projects of all sizes, scope and complexity across the country in a wide range of markets including stadiums and casinos, data centers, K12 and universities, hospitals and medical centers, concert halls and casinos, manufacturing facilities and power delivery.
###
CONTACTS:
Gina Swanson
[email protected]
612.298.2631
Angela Mork
[email protected]
651.602.6538
Categories: News Releases